Home Assistant Heating Controller
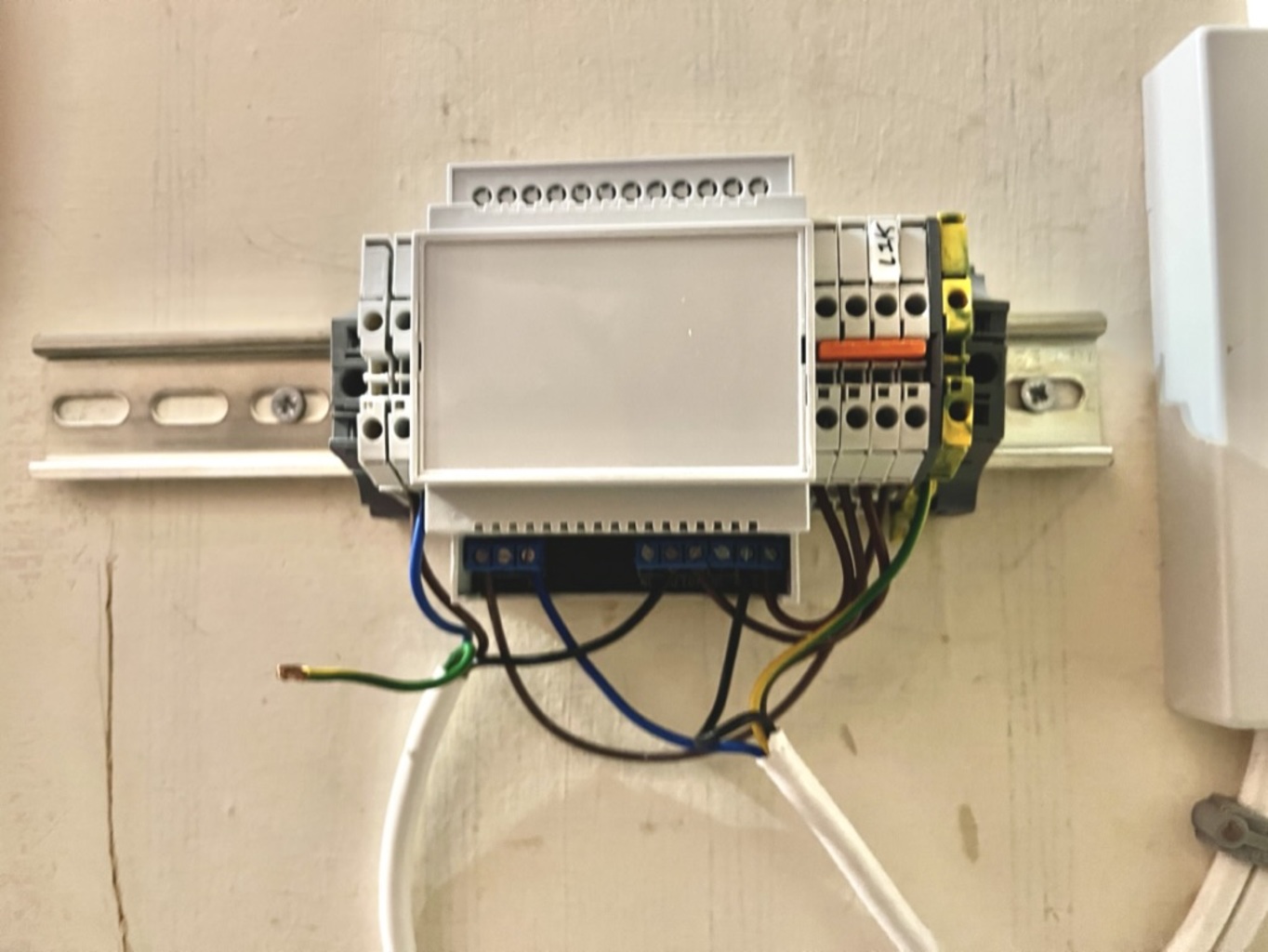
Motivation
I’ve been using Home Assistant to automate my house, and one of the big things I want to add control of is my heating. The heating system in my house is a little different to a typical British home in that I have zones, one for upstairs (radiators) and one for downstairs (underfloor heating). This means a lot of the off-the-shelf thermostat options, especially Google Nest, aren’t suitable for me, and what options there are have a prohibitive cost.
A commercial option would be something by Hive, they support multi-zone thermostats, and they are supported in Home Assistant. Sadly, this option would cost about £300.
Home assistant to the rescue, it has a built-in integration for
controlling heating, so long as you provide it a switch to toggle the
heating, and a sensor to read the current temperature. It even has a
nice interface.
My boiler
What are we contending with? I have a combi-boiler hooked up to a pair of Honeywell thermostats.1 Both thermostats are set up to bridge the ‘request for heat’ control line on the boiler. Here’s what the thermostat receiver looks like for my underfloor heating.
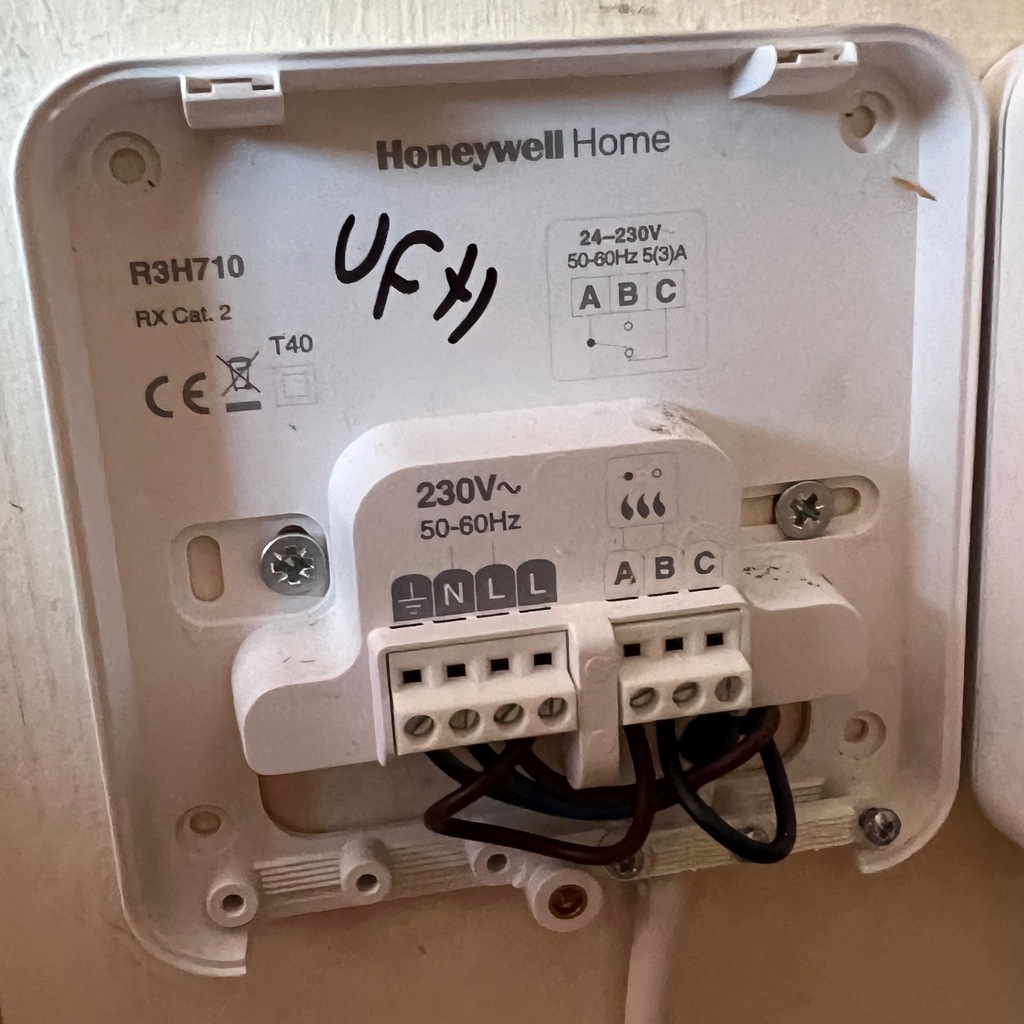
This interface is pleasingly simple, the controller mounts on top and
simply has an RF receiver for the thermostat, and a relay to bridge
connect A
to B
. To connect this to home
assistant I could just use a generic relay board, like this from Amazon, and
flash the ESP8266 with ESPHome.
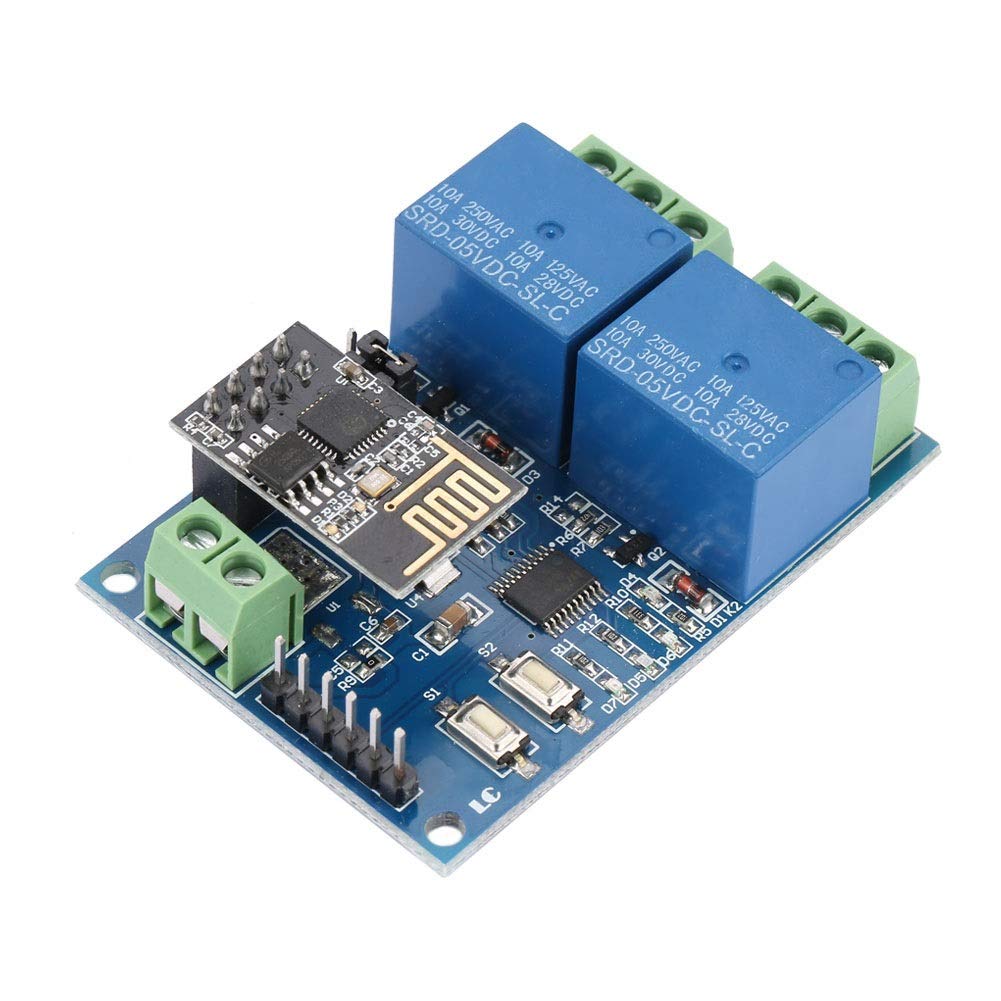
This solution doesn’t please me, though. I’d need to separately have a mains to 12v power supply to control something which is switching mains voltage. A quick search didn’t yield anything satisfactory with an integrated power supply, so I am left with only one reasonable choice: build my own at significant expense and time cost, negating any cost saving from not buying the expensive Hive thermostats in the first place. Okay, it’s not quite that bad, the BOM for each of these boards comes to about £50 in small quantities, so it’s still a lot cheaper, and it can probably be optimised a fair bit. And no price can be put on the enjoyment I get when designing a PCB.
Enclosure
First thing’s first: the enclosure. I recently scavenged a bunch of DIN mounted hardware from an old CNC machine control panel, and I quite like DIN mounting. A scan of Farnell yielded this bad-boy:
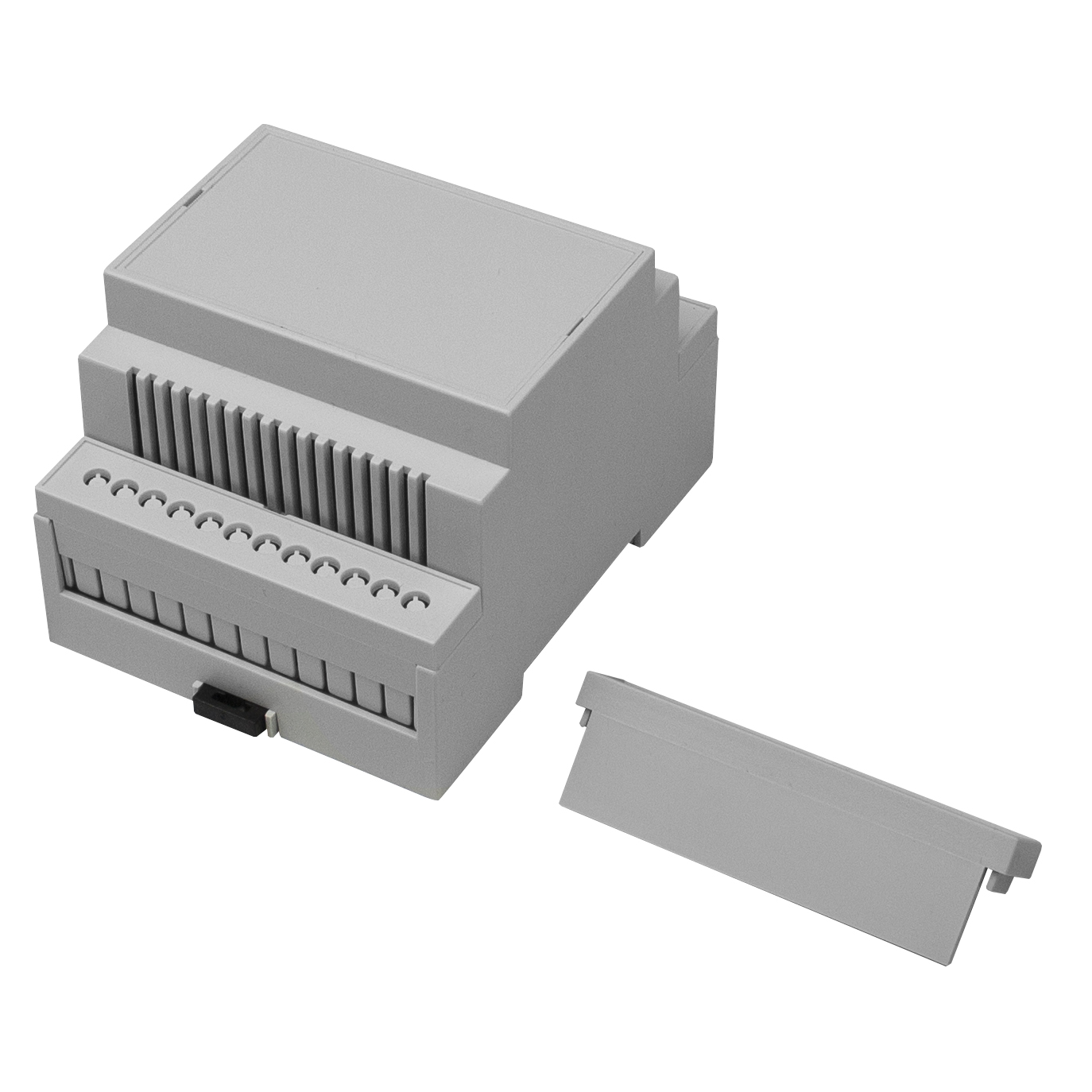
This supports a reasonable 86.5x68mm PCB in the bottom-most mounting position.
Circuit design
I need three key things on this board:
- Power supply, mains to a reasonable DC voltage for some relays
- ESP8266/ESP32 compatibility
- Two relays, one for each of my heating zones
I did all the design in Eagle, the CAD files are available here. They are provided without warrantee, I’m not a qualified electrical/electronic engineer. If your house burns down it’s between you and your insurer.
Relays
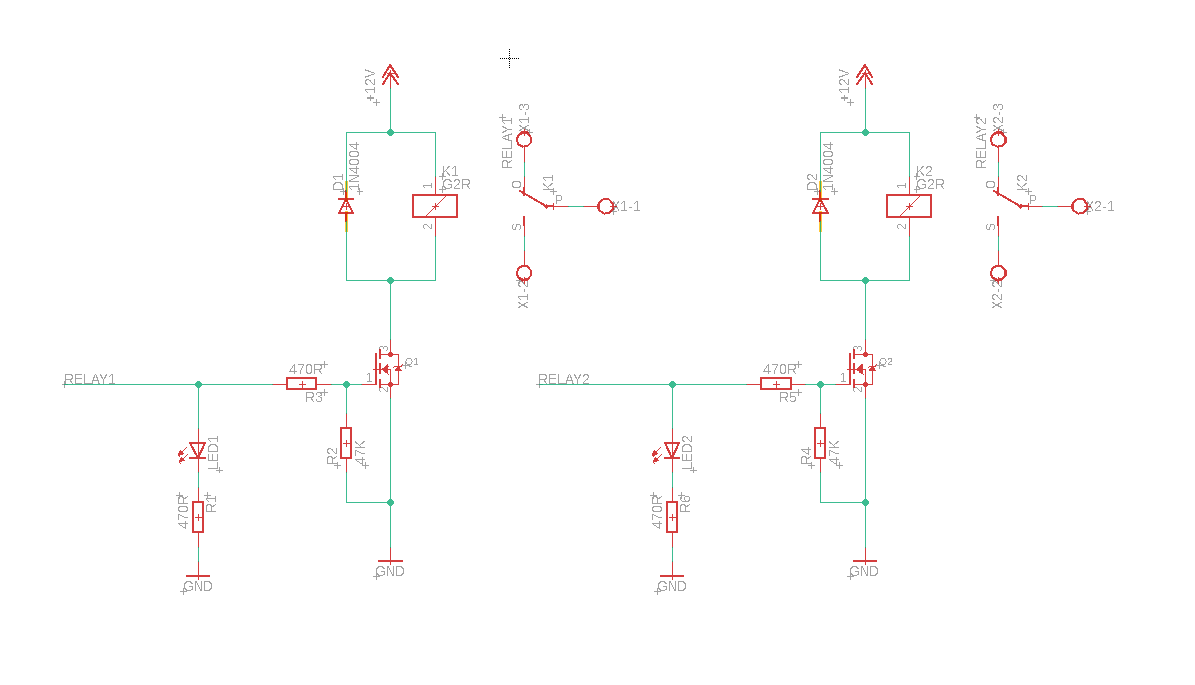
This is basically a text-book circuit. I’m using 2N7002 MOSFETs to control the coil on a relay, these FETs are great as they have a very low trigger voltage of about 1v (ideal for 3.3v logic).
Power supply
This was by far the most difficult part to deal with. I didn’t want to roll my own AC/DC converter or switch mode power supply, so I picked a PCB-mount module. The first one I selected was very simple, but regrettably £20 ea. I thought about it and decided to deal with a SIP module with a higher integration complexity (and board footprint), but that was substantially cheaper at £1.86 ea, and about £5 in support components. The various filter components are what are recommended by the data sheet.
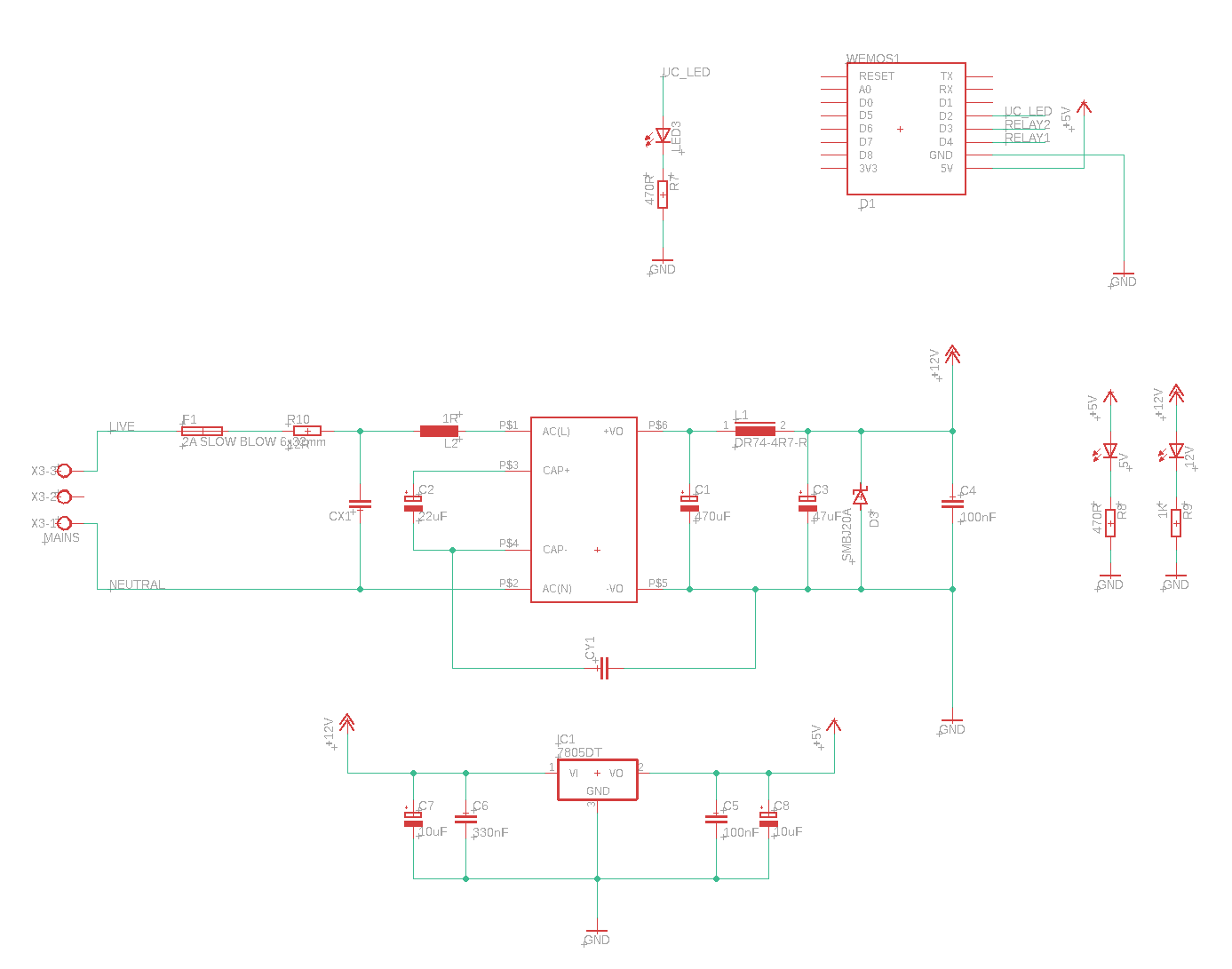
In theory, I should also add MOV between L and N, but this is optional in the data sheet’s application note, and the board I have is quite well populated. Maybe in REV2.
PCB
I got the PCB made by JLCPCB, the same one from all the YouTube mid-roll adverts… I’m very impressed, it came quickly and appears to be exactly what I asked for including semi-complicated routed slots! There was no extra cost for the black solder mask, but there was an extra one-day lead time. From design to PCBs in-hand was about 2 weeks, as I paid for slower (cheaper) shipping. Total cost for 5 boards (which is the minimum order) was $14. So about £10.
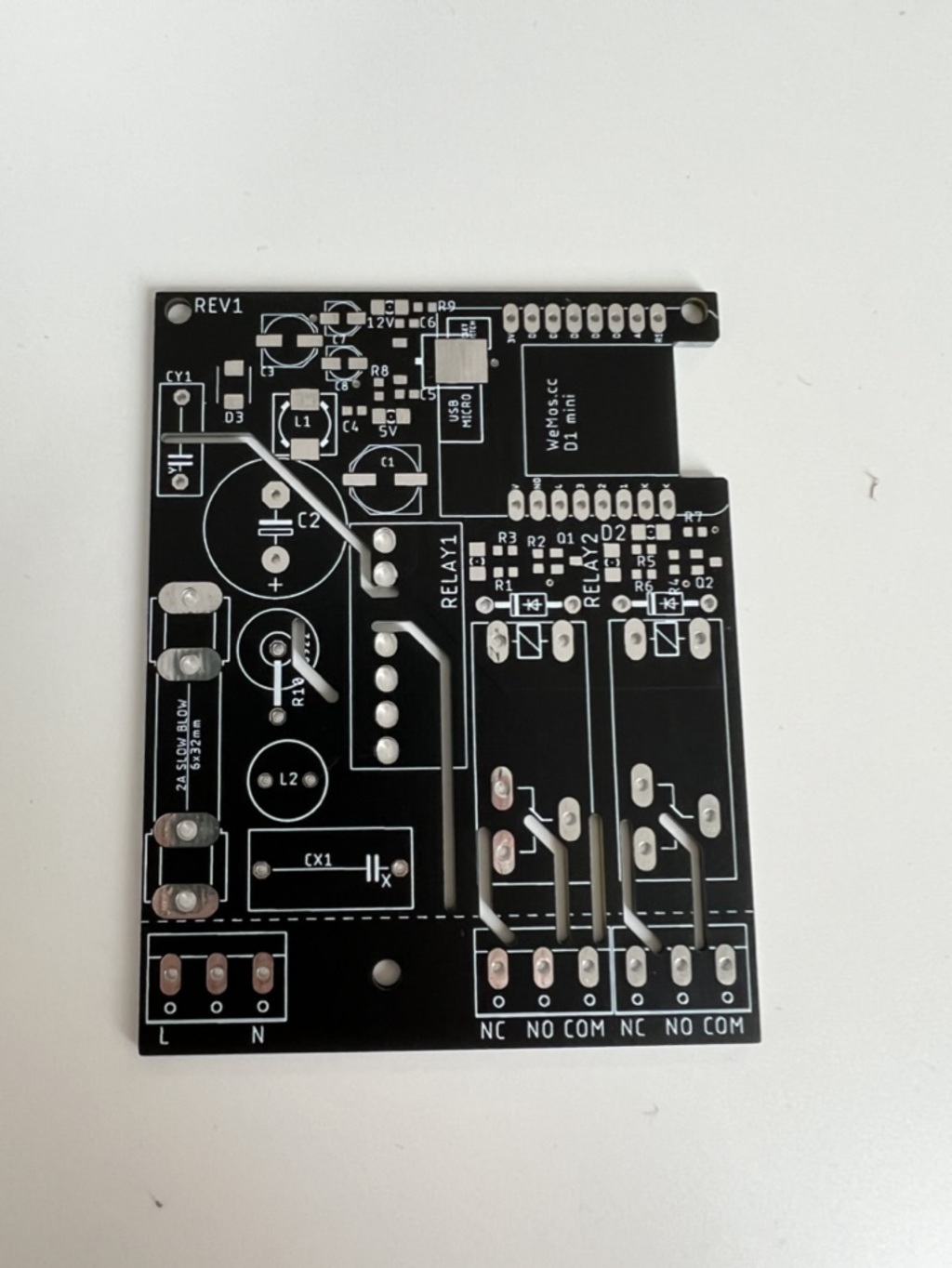
ESPHome setup
ESPHome is fantastic for DIY smart home gadgets. With just a familiar
(at least to Home Assistant users) YAML configuration you can create a
binary to run on an ESP32, ESP8266, etc, which will connect to your
Wi-Fi and expose all manor of sensors and actuators to your Home
Assistant API. This project is wildly simple for ESPHome configuration
and comprises simply two switches connected to D3
and
D4
of the D1 mini. There is also a status LED on
D2
.
esphome:
name: "heating-controller"
esp8266:
board: d1_mini_lite
# Enable logging
logger:
# Enable Home Assistant API
api:
ota:
light:
- platform: status_led
name: "Heating status"
pin: D2
switch:
- platform: gpio
pin: D3
name: "Underfloor heating"
- platform: gpio
pin: D4
name: "Radiators"
wifi:
ssid: !secret wifi_ssid
password: !secret wifi_password
# Enable fallback hotspot (captive portal) in case wifi connection fails
ap:
ssid: "Esphome-Web-0C2621"
password: "3Hkntq3KmOXA"
captive_portal:
It works!
Remarkably, notwithstanding a few minor bugs, the board worked first time!
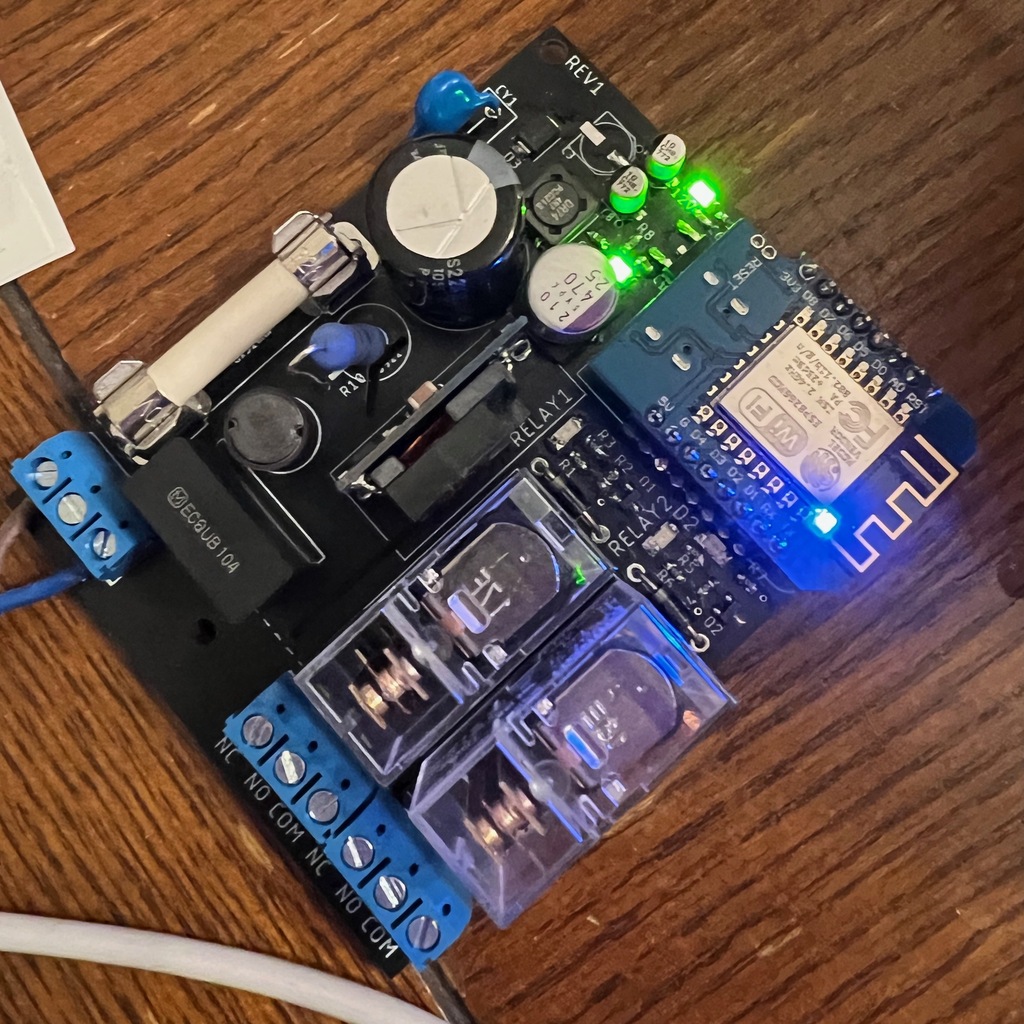
Now I just need to wire it up to my boiler.
Bugs with REV1
The footprint for C1 was one size too small, the Panasonic-F
capacitor barely fit on the E-pad. I also forgot to buy the lower value
output filter capacitor for the 12V PSU, so that’s unpopulated on my
board. I bought the wrong size fuse holders, but they just about worked
for the 32x6mm fuse. The D1 mini has a bright blue LED on
D4
, so moving Relay 2 to something else would be
better.
There are two mechanical issues. The clearance for the D1 mini is not good, it interferes with an internal support on the CMMB/4 enclosure, so it needs to be moved a few millimetres to the west. The terminal blocks are not well aligned with the holes on the cover for the CMNB/4 enclosure, they need to move south and towards the centre.
Next revision
Apart from fixing the REV1 bugs there’s a couple of things I would do differently in a future revision.
I’ll add a couple of pads for connecting a thermal probe, this will make the board useful to people with a water cylinder, especially those who want to automate using solar energy to keep their water hot when possible. As far as I know, most water cylinders in the UK have two heating elements one top, one bottom, so the dual relay will be useful for that. I might put the ESP on a daugter-board with a screen for status, and the status LEDs broken out more sensibly. This will free up a bit of space on the bottom board nicely, and fix that mechanical issue.
There’s some minor tweaks to do to the power supply too. Adding a MOV and a bleed resistor would add a couple of extra types of safety.
Bill of Materials
Part IDs | Value | Package | Part description |
---|---|---|---|
Enclosure | – | CMNB/4V/Kit | DIN Mount enclosure |
C1 | 470µF | Panasonic E | 12V PSU output capacitor |
C2 | 22µF/450V | 16mm radius | Mains input cap |
C3 | 47µF | Panasonic D | 12V PSU output capacitor |
C4, C5 | 100nF | 0603 | Linear regulator decoupling |
C6 | 330nF | 0603 | Linear regulator input capacitor |
C7, C8 | 10µF | Panasonic B | Linear regulator bulk capacitance |
CX1 | Class-X | 15mm | Class X mains input capacitor |
CY1 | Class-Y | 10mm | Class-Y mains input capacitor |
D1, D2 | 1n4004 | DO41 | Relay flyback diode |
D3 | SMBJ 20V | SMBJ | Over-voltage protection shunt diode |
F1 | 2A | 6x32mm | Fuse, slow blow |
IC1 | 7805 | TO252 | 5V linear regulator |
K1, K2 | G2R-12 | Omron 12VDC relay | |
L1 | 4.7µH | Radial 5mm | 12V PSU output filter inductor |
L2 | 1mH | DR74-4R7-R | Mains input filter |
LED1, LED2, LED3 | Green | 1206 | LED |
Q1, Q2 | 2N7002E | SOT-23 | N-Channel MOSFET |
R1, R3, R5, R6, R7, R8 | 470R | 0603 | Resistor |
R2, R4 | 47K | 0603 | Resistor |
R9 | 1K | 0603 | Resistor |
R10 | 12R | 22mm, 3W | Resistor |
SIP | – | MP-LS05-13B12R3 | AC/DC converter 12V |
The schematics and layout are available on my GitHub.